Services
Transformer Healthcare Package
Transformer Dryouts & Oil Processing
LTC Retrofit
Case Study – Transformer Refurbishment
Transformer Regasketing
LTC Fleet Assessment Program
Transformer Life Extension
Performing transformer life extensions (TLEs) is the practice of improving and upgrading an asset, returning it to near new status. TLEs provide a strategic fleet management option to overcome issues with budget, availability, site constraints and/or grid priorities. Current supply chain constraints and longer lead times magnify these issues, making TLEs a viable option for more asset managers.
As defined here, TLEs are done to upgrade and improve critical systems to add useful life to the asset. In contrast, a transformer rewind would be considered a full transformer rebuild. A rebuild is normally considered when a catastrophic event happens in the main tank and the unique nature of the asset requires a like-for-like replacement of the unit. Rebuilt units also serve as a viable alternative on the secondary market.
A TLE is an option when the main tank elements (core and coil) are in excellent shape, and the peripheral elements are contributing to the asset’s limitations. For example, an ideal transformer for a TLE would have DGA and electrical tests on the main transformer tank which indicate a healthy unit, but its arcing-in-oil load tap changer (LTC) is a potential failure point. In this instance, the main tank is healthy and could provide several years of additional service to the utility; however, the LTC’s condition may force a premature retirement of the asset.
Each utility will have its own process for evaluating assets and determining which assets are TLE candidates, but the four main considerations are as follows:
- Unique designs and location constraints
- Health of the candidate units
- Asset classification
- Fleet status and availability of new units
When the design of the existing unit or substation does not allow for a change in footprint, a TLE may be the only option. For these assets, TLEs can help overcome physical constraints. In urban areas where transformers can be located inside structures, replacing a transformer can pose significant challenges.
New designs can change the height, width, or length dimensions, changes that may not conform to existing codes. If the main tank is viable, a TLE will allow the asset to be upgraded in place. Managing the TLE within the existing footprint can eliminate the need for a new substation project.
The health of the main tank is the primary driver when considering a TLE. You should evaluate trend data as well as point-in-time reports to determine the viability of the unit. Both DGA and routine electrical tests should be evaluated. Additional data can also help evaluate the health of the unit, including fault history, PD monitoring data, surge counts, historical load profile, etc. Once the data analysis is complete and the unit is determined to be a candidate, a visual inspection should be performed to determine if any internal issues exist. The decision to perform a TLE is subjective, and each utility will have a threshold for the minimum acceptable condition to move forward.
Two Primary Considerations: Accounting Treatment and Economic Viability
Each utility will have a lower and upper bound for TLEs. The lower bound may be driven by accounting and asset management rules that prescribe the minimum requirements for capitalization of the project. These requirements can be expressed in terms of dollars vs. asset value or in terms of the number of systems addressed. Accounting principles must be considered as well as regulatory requirements and PUC rate case requirements when establishing parameters to evaluate capital reinvestment in an existing unit.
The upper bound is the crossover point where investment in the existing asset no longer makes financial sense. With any capital project, there will be a cost/benefit calculation. Generally, the viability of the TLE diminishes as the value of the upgrades approaches the value of a new asset. Certain assets will not warrant a TLE. The cost of updating an older asset compared to the cost of a new asset and the ability to establish a longer depreciation schedule on the new asset will naturally drive a decision for the new asset.
Situations exist where the status of the utility fleet, spares, and upcoming expansion projects will influence the TLE decision. When the available budget or number of assets becomes finite and the current assets outstrip available resources, extending the life of existing assets can overcome the shortfall. This can be a temporary strategy to minimize the impact of point-in-time conditions, or it can augment a new unit strategy. TLEs allow utilities to manage expansion, non-viable unit replacement, and service levels to customers.
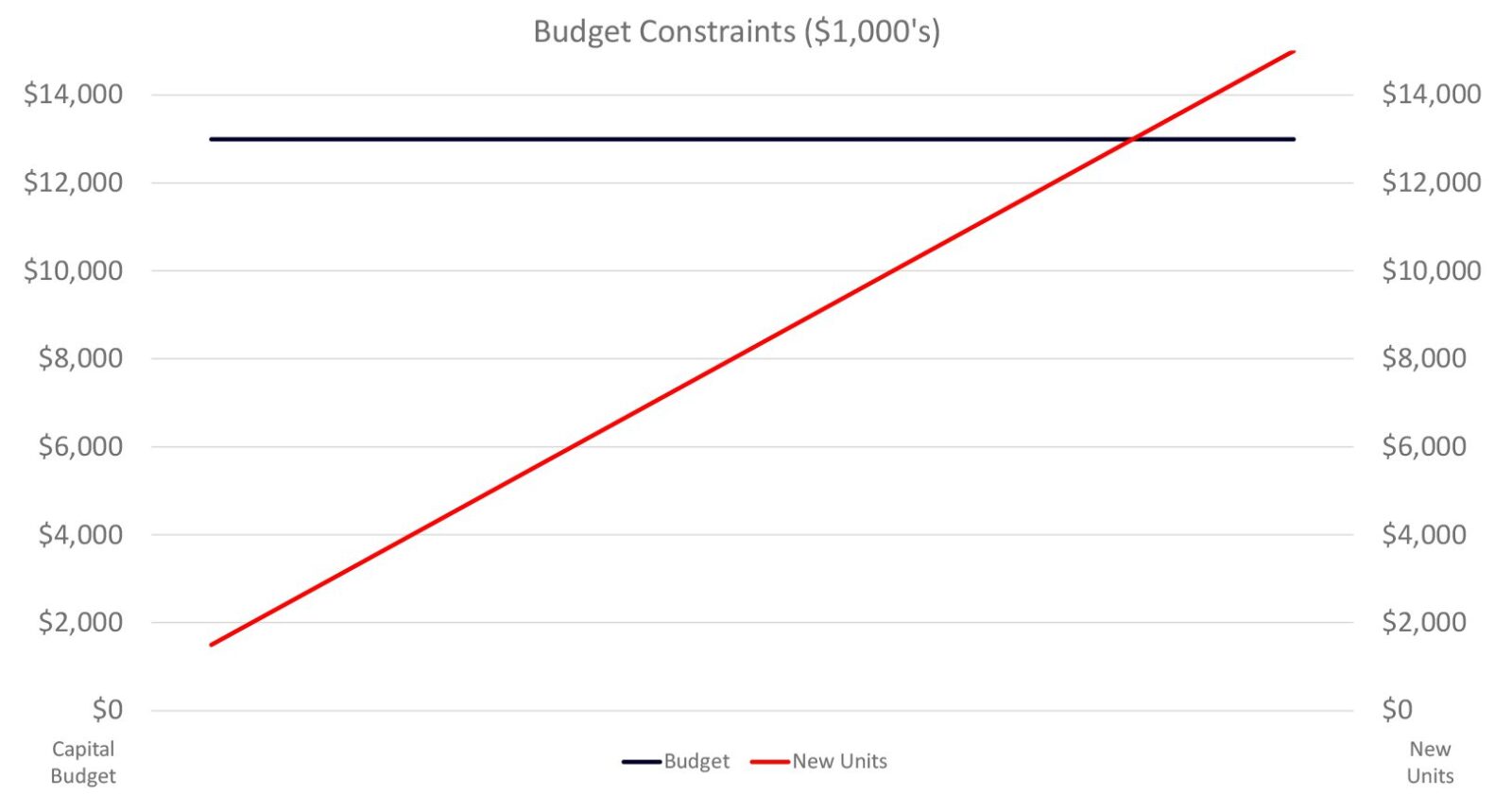
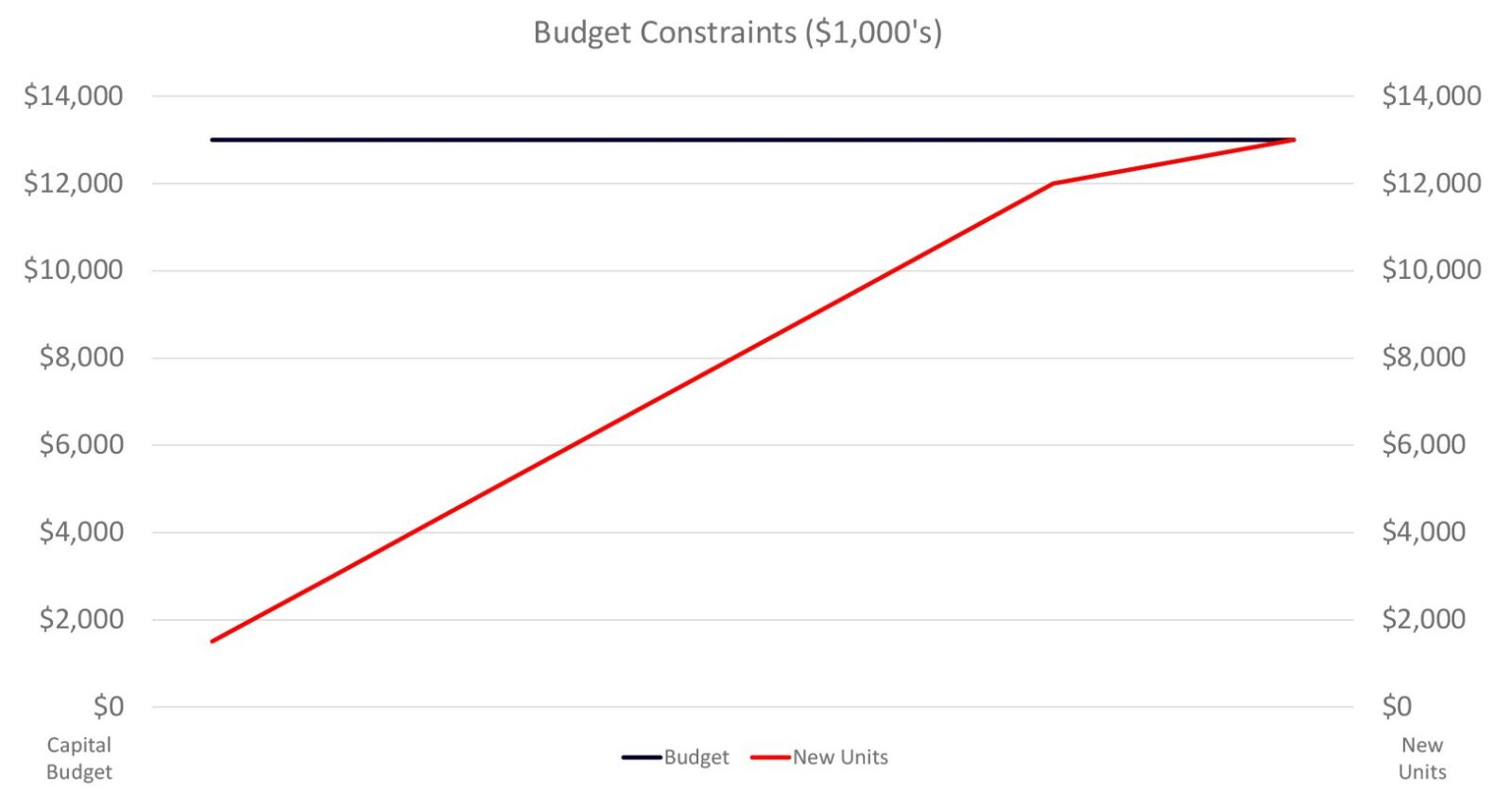
Once assets are evaluated and identified for TLE, scope of work elements are identified. Each utility will have its own process for evaluating the elements to include in a TLE, but here are six considerations:
- Load tap changer: upgrade or retrofit
- Electrical controls: wiring, terminal blocks, gauges, fuses, relays, breakers, and heaters
- Electrical load handling: bushings, arresters, and leads
- Fluid cooling and breathing: radiators, fans, pumps, coolers, conservator, and breathers
- Monitoring and controls systems: alarms, protection, and asset monitoring
- External tank upgrades: painting, crack repair, and leak mitigation
LTC Updates
One of the weakest systems on a transformer is the LTC. The LTC is a common—and often catastrophic—failure point. Arcing-in-oil units require periodic inspection and maintenance to ensure proper operation, and older vacuum systems do not benefit from the design improvements realized over the last 50 years. Moving from either of these systems to newer technology can extend the life of the transformer and minimize ongoing maintenance costs. Retrofitting the LTC with a new vacuum unit is a significant upgrade to the transformer. However, the ability to upgrade to new vacuum technology depends on the design of the transformer. Each unit must be evaluated and inspected to verify the unit qualifies for an LTC retrofit. Once validated, a complete set of engineering drawings is produced to include the new vacuum LTC. The LTC retrofit is a significant project that can take 30+ weeks from identification to commissioning; however, the total transformer outage time to perform the upgrade is typically only two to three weeks, including LTC throat wall retrofits.
Transformers that utilize outdated, maintenance intensive vacuum tap changers also benefit from upgrades that take place during transformer life extensions. First generation vacuum systems may require more frequent maintenance or adjustment to perform properly. Current generation LTCs improved the reliability of the systems, but older units may require upgrade or replacement to overcome limitations of the earlier designs.
Controls Upgrades
Electrical controls within the transformer are frequently upgraded during the life extension process. Gauges that monitor performance of the unit’s temperature, pressure, tap position, and fluid level are replaced with modern equivalents that have outputs for external monitoring. Control cabinets on field-aged transformers normally have multiple modifications performed by field crews that sometimes render the original control drawings inaccurate. The life extension process involves a reengineering effort that can include replacement of control cabinet wiring as well as components within the control cabinet of an outdated design that are no longer produced, such as fuses and terminals.
Heaters in the control cabinet along with relays and breakers used for auxiliary power handling are frequent sources of unplanned maintenance for field personnel during inspections on aged assets. The TLE investment offers replacement of these 20 to 50-year-old electrical items. Replacing the auxiliary control devices also provides the opportunity to decrease auxiliary voltage from 480V to 240V to accommodate modern safety practices that require arc flash protective equipment for 480V environments.
Electrical Load Handling
Bushings can also be upgraded as part of the TLE process. Due to their flammability, oil-impregnated paper (OIP) bushings can cause significant damage to other components, the main transformer, and even other systems in the substation. Upgrades to resin-impregnated paper (RIP) bushings can provide lower partial discharge, zero headspace, better physical characteristics, and are non-flammable while also offering lower external current leakage and reduced risk of flashover in contaminated coastal environments. Utility design parameters and preferences will influence adoption of this technology; however, a retrofit with RIP bushings can provide an upgrade to the transformer.
External arresters used for lightning and over voltage protection are normally replaced during the TLE upgrades. Aged porcelain-insulated arresters are frequently upgraded to new polymer sheathed designs that offer better performance in industrial and coastal environments. System conditions normally evolve during a transformer’s life cycle, which could provide an opportunity to optimize the arrester’s maximum continuous operating voltage, fault magnitude, and energy ratings for current requirements. Lower temperature operation along with replacement of the bolted electrical connections will reduce arrester maintenance and call-out visits in the future.
Improved Cooling Performance
Upgrades to the cooling system offer multiple benefits to the life of the transformer. Both fans and pumps are rotating assemblies and performance can degrade or fail over time. Upgrading to new fluid handling equipment will help restore the cooling capabilities originally designed into the transformer. In addition to ensuring all components are working, upgrading to modern, higher CFM, lower amp draw, sealed bearing fans—or even adding fans to the system—will help maintain operating temperatures in the main tank. Pump performance is also critical to maintaining the appropriate cooling.
Radiators used in transformer construction evolved from tube-based designs to more efficient plate-based coolers. Radiator performance increases from header pipe design, cooler efficiency, and cleanliness might add years to the life of a field-aged transformer. Modern radiators are more durable with longer lifespans, and most are zinc-coated to further extend life. Radiators will be replaced as part of a scheduled TLE.
Replacement of the conservator bladder, the Buchholz relay, and sudden pressure relay will restore the transformer’s oil handling and fluid-based protection systems. Leaks in the rubber conservator bladder increase moisture contamination within the transformer’s main tank and cause premature degradation of
in-tank insulation. Breathers are often upgraded to self-drying models to reduce O&M costs associated with replacing desiccant. If the transformer is nitrogen blanketed rather than a conservator design, replacement of the cylinder regulator and cylinder itself will be evaluated along with the potential addition of a nitrogen generator system.
Monitoring
The addition of real-time monitoring equipment as part of a TLE upgrade provides the transformer owner the opportunity to reduce maintenance visits. Gas-in-oil monitoring, partial discharge, remote temperature outputs, and bushing monitoring are useful additions to consider when performing a proactive life extension. Trending data that can be accessed remotely helps identify issues early before a critical failure occurs.
External Considerations
Aged transformers frequently suffer from fluid leaks and external tank degradation, such as rusting and welding cracks. The re-gasketing of fluid handling equipment on the transformer during a TLE might also include an external inspection that results in a recommendation to paint the outside of the transformer’s main tank. In salt air contaminated environments, paint deterioration is a frequent maintenance item that can be greatly improved with a deep cleaning and full “top to bottom” recoating. Failed welds and joints can be repaired on-site to decrease future maintenance visits and third-party contractor expenditures.
With a proactive and calculated approach to TLEs, a utility can improve the overall quality of its fleet. TLEs can provide reductions in forced outages, unit failures and maintenance. They can also improve quality of service, maximize spend, and allow for greater flexibility when dealing with spares and expansion. Transformer life extensions are another tool to ensure the reliability of the grid and high service levels while adding years to the life of the assets.
After the life extension, you could have:
- Solid main tank (tested and inspected prior to project)
- Modern load tap changer (a weak link in transformers with arcing-in-oil or early vacuum LTCs)
- New controls and information devices
- Improved electrical load handling (potentially safer and more reliable than existing equipment)
- Better cooling performance
- Upgrades to real time monitoring, and
- Refreshed externals